内检测作为完整性管理的重要组成部分,是管道安全运行管理的必要手段。本文针对某成品油管道环氧粉末防腐层发生大面积剥离现象,基于完整性评价漏磁内检测、外检测等数据进行腐蚀情况分析,排查管道发生腐蚀的重点管段,以采取有效措施,降低管体腐蚀风险。
1 管道腐蚀概况
某成品油管道于2004年投产,全长228?km,管材为X60钢,管径426?mm,壁厚7.0?mm,外防腐层为熔结环氧粉末涂层(FBE),在里程4.8?km处首站油库及里程64?km处分别设置一座阴保站。在管道内检测开挖验证、本体修复及其他开挖项目实施过程中,发现环氧粉末涂层出现大面积剥离,管体表面发生锈蚀,存在不同程度的腐蚀坑,见图?1。环氧粉末涂层对施工工艺、施工环境等有较高要求,如出现管体喷砂打磨等表面处理不达标,环氧粉末双组分混合比例不合格,施工温度低于水露点等情况,容易造成防腐层质量不合格,给管道带来较高的腐蚀风险。
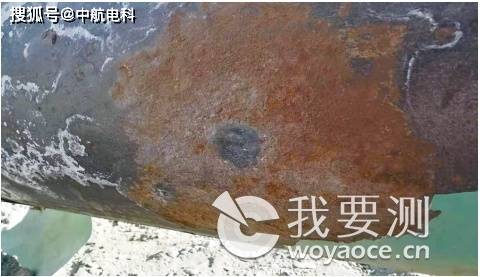
图 1 管体腐蚀情况实景图
2 防腐层检测分析
2.1 防腐层PCM检漏情况
使用PCM(交流电流衰减法)进行防腐层破损点检测,全线共检测出防腐层缺陷点2655处,平均11.6处/km,按照外防腐层缺陷点密度分级评价,防腐层等级为3级。首站油库-2#阀池的长度约22.28?km,防腐层破损点383处,平均17.2处/km,其中22处评价为重,321处为中、40处为轻。
2.2 防腐层性能分析
(1)表面处理情况分析。管道建设期,为提高防腐层的黏接力,在涂敷防腐材料前需对管体表面进行处理,根据SY/T?0315―2013《钢制管道熔结环氧粉末外涂层技术规范》相关要求,表面锚纹深度应在 40?μm~100?μm。去除剥离的防腐层,测量管体锚纹深度,检测结果如表?1所示。可见,锚纹深度不符合标准要求。
表 1 管体锚纹深度测试结果
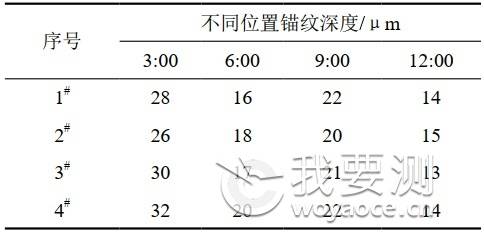
表 2 环氧粉末玻璃化转变温度统计表
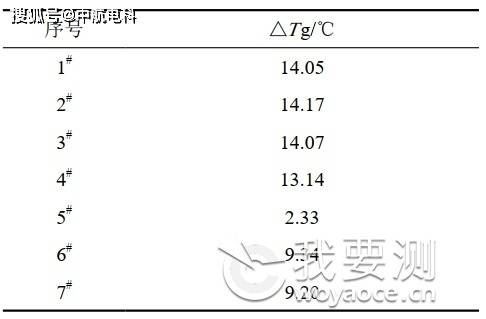
固化温度是保持FBE涂层长效附着力的关键,低于标准温度下的固化不利于熔融态分子对底材的浸润。根据GB/T?39636―2020《钢制管道熔结环氧粉末外涂层技术规范》要求,玻璃化转变温度△Tg应大于最高使用温度以上40℃。选取7处FBE涂层材料进行热特性试验,结果如表?2所示。可见,材料玻璃化转变温度不符合标准要求。
选取典型腐蚀产物样品,进行XRD检测,分析锈层中各成分含量情况,结果如图?2所示。

图 2 腐蚀产物XRD谱图
XRD结果表明主要腐蚀产物为NaHCO3和Fe3O4,因管道表面土壤为碱性土壤,测试现场土壤电阻率为570?Ω·m,pH值为10,土壤腐蚀性较弱,并非加速管道发生腐蚀的主要因素。
3 阴极保护效果分析
2014年该管道开展ECDA(外腐蚀直接评价)检测,CIPS(密间隔电位法)检测结果(图?3)显示,里程3?km~6.5?km管段断电电位负于﹣1200?mV(CSE),处于过保护状态;17?km~55?km管段及80?km~112?km的部分管段断电电位正于或接近﹣850?mV(CSE),无法达到阴极保护状态。通过测量全线管地电位发现,5#测试桩处首站油库阴保站出站电位为﹣1.998?V,33#测试桩处电位衰减为﹣0.730?V,表明管道阴极保护电流衰减严重。
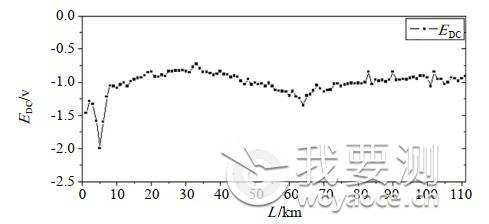
图 3 成品油管道0~110 km电位曲线图
两座阴保站的恒电位仪运行参数如表?3所示。经测试,阴保站恒电位仪输出正常,阴极电缆、阳极电缆、参比电缆、零位接阴电缆完好,参比电极工作正常。首站油库阴保站恒电位仪输出电流已高达10.1?A,但距离该阴保站仅12?km的管道阴极保护电位仍然偏正。
表 3 2014年阴极保护系统运行参数统计表
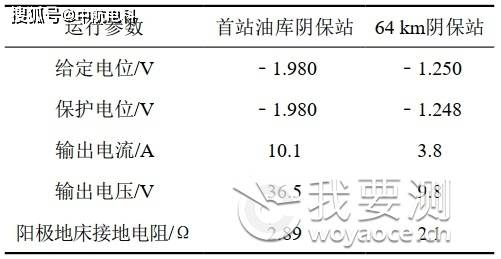
通过对防腐层、阴极保护电位及恒电位仪输出情况进行梳理分析,靠近首站油库阴保站管段电位过保护,而远离阴保站管段电位欠保护。因此,靠近首站油库阴保站管段防腐层较差,破损点较多导致阴极保护电流流失严重是重要原因。
4 漏磁内检测结果分析
为掌握管道真实的腐蚀状况,2019年对该管线开展漏磁内检测,共发现管体金属损失9303处,大于20%?wt金属损失共计163处,其中内部金属损失40处,外部金属损失123处。通过开挖验证,本次内检测精度及可信度均满足要求。
为排查全线管道外腐蚀风险重点管段,按照每20?km长度划分出11个管段,统计大于20%?wt外部金属损失数量和比例。其中首站油库—20#测试桩管段大于20%?wt金属损失数量远多于其他管段,占全线的84.6%。该管段腐蚀深度较大,超过50%?wt外部金属损失有3处(表?4)。
表 4 首站油库—20#测试桩管道外部金属损失情况

通过上述分析可以看出,首站油库—20#测试桩管段外部金属损失数量多、腐蚀深度大,是外腐蚀风险的重点管段。
5 处置对策及效果分析
针对该外腐蚀风险重点管段,2016—2021年,对首站油库—27?km处管段采用无溶剂环氧涂料开展了防腐层大修。2017在里程32?km处新增一座阴保站,为管道提供阴极保护电流。
为评估防腐层大修和新增阴保站对阴保系统的影响,统计首站油库和64?km处两座阴保站阴保测试数据(表?5),与表?3防腐层大修前数据对比。
表 5 2022年阴极保护系统运行参数统计表
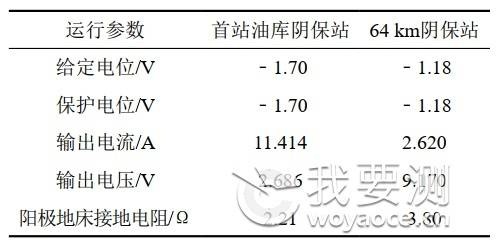
可以看出,32?km处阴保站恒电位仪投用后,首站油库及64?km阴保站恒电位仪输出明显下降,输出电流分别由10.1?A和3.80?A下降至2.686?A和2.62?A。新阴保站的投用降低了其他阴保站恒电位仪负荷,共同对管道实施阴极保护。另外,防腐层大修后提升了管道防腐层的完整性,有效减少了阴极保护电流衰减。
2019年,ECDA项目对管道断电电位进行了测量,其通断电电位趋势如图?4所示。结果表明,2014年ECDA检测时断电电位正于或接近﹣850?mV(CSE)的管段,在增设32?km处阴保站和防腐层大修后,其断电电位均满足负于﹣850?mV(CSE)准则要求,达到阴极保护目的。
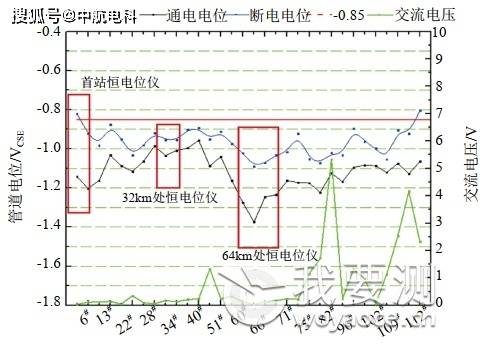